The manufacturing industry is undergoing a seismic transformation. Is this the next Industrial Revolution? Perhaps. One thing is certain: modern manufacturing processes are evolving rapidly, blending cutting-edge technologies like AI, robotics, and the Internet of Things (IoT). These advancements are driving efficiency, reducing waste, and enabling manufacturers to meet growing global demands.
But this isn’t just about technology. It’s about solving the complex puzzle of balancing growth with environmental sustainability. How can companies adapt? The answer lies in Industry 4.0, where innovation meets responsibility, offering tools and strategies to thrive in this new industrial era.
What is Industry 4.0? Think of it as the next stage in manufacturing evolution, where technology does more than support processes—it transforms them. With IoT, big data, and real-time analytics, manufacturers are not only increasing output but also reducing their carbon footprint. But the journey to this point has been anything but linear. Understanding how the industry arrived here offers valuable insights into where it’s headed.
What is Industry 4.0?
Industry 4.0 represents a fundamental shift in the way industries operate, leveraging advanced technologies to boost efficiency, flexibility, and sustainability. It’s often called the Fourth Industrial Revolution, but what makes it revolutionary?
At its core are four essential components:
- IoT (Internet of Things): This network of interconnected devices ensures seamless communication across the factory floor. IoT doesn’t just improve coordination—it enables predictive maintenance, enhances safety, and optimizes workflows.
- Smart factories: These highly automated facilities rely on self-regulating systems, reducing waste while maximizing productivity.
- Big data: By analyzing large volumes of data, manufacturers uncover trends, address inefficiencies, and identify opportunities for innovation.
- Real-time analytics: Instant data processing allows manufacturers to respond quickly to challenges, reducing downtime and improving agility.
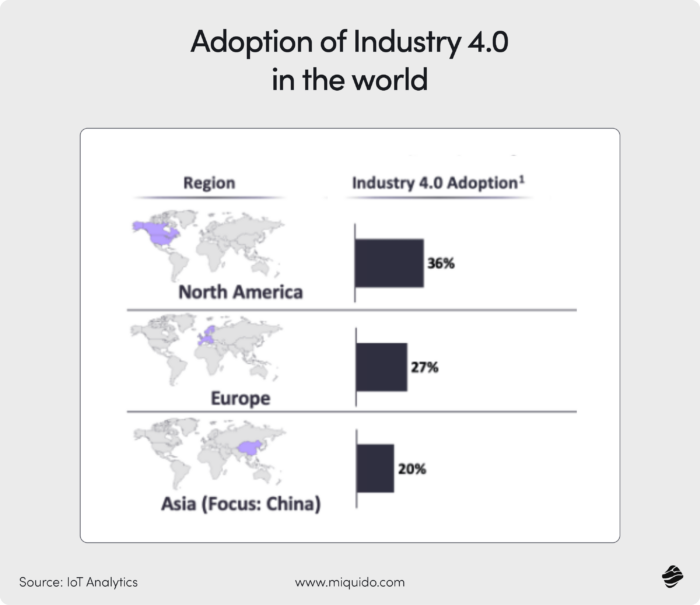
Together, these components redefine how manufacturing facilities operate. With IoT ensuring connectivity, big data driving insights, and real-time analytics enabling instant action, companies embracing Industry 4.0 are more competitive and adaptable. But implementing these technologies effectively requires a strategic approach, as they are not without challenges.
The world has been quick to adopt Industry 4.0 principles, though some regions lead the charge. For instance, North America boasts the highest adoption rates, followed by Europe and parts of Asia.
The main goal? It hasn’t changed since the dawn of the Industrial Revolution. Manufacturers aim to produce more and better at lower costs. Industry 4.0 brings them one step closer to achieving this if implemented correctly. However, with the growing understanding of climate and pollution issues, the pressure to reduce environmental impact is strong. The technological tools essential to Industry 4.0 help companies marry these two potentially conflicting goals.
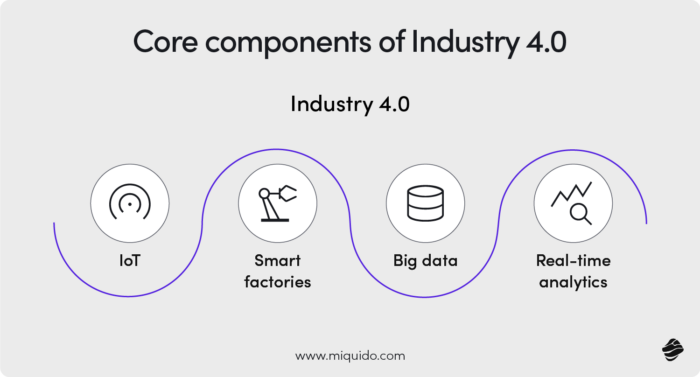
From traditional manufacturing facilities to industry 4.0: A timeline
How did we get here? To understand Industry 4.0, it’s worth looking backward. Modern history’s twists and turns have shaped the path of the manufacturing industry and defined the pace of its evolution.
First, the post-war growth and the booming wealth and consumption in the global West pushed manufacturing methods forward while intensifying environmental impact due to mass production. The energy crises of the 1970s brought the first sustainability-oriented changes to the table, although renewable energy integration remained slow.
The development of computer science was behind manufacturing’s next big leap, leaving outdated old line industry behind. The expansion of the internet and computing power carried it forward in the following decades, with AI opening doors that had been closed to date.
Here’s a look back at key milestones that shaped the industry in the last 20 years:
- 2004: Emergence of IoT (Internet of Things) in industrial settings, enabling smart factories and connected devices.
- 2010: Launch of High-Tech Strategy 2020 in Germany, formally popularizing the concept of Industry 4.0.
- 2014: Launch of the Industrial Internet Consortium (IIC) to promote IoT in manufacturing sectors.
- 2016: Breakthroughs in 3D printing bring additive manufacturing into mainstream industrial applications.
- 2019: Development of blockchain solutions for supply chain transparency and manufacturing integrity.
- 2020: The COVID-19 pandemic accelerates the adoption of remote operations and automation across industries.
- 2022: The introduction of EU ESG norms which oblige companies to report of CO2 emissions across the whole supply chain, calling for advanced tracking and reporting solutions.
- 2023: Expansion of GenAI in manufacturing, enhancing product design, predictive analytics, and customer personalization.
- 2024: Breakthroughs in quantum computing prototypes show potential for optimization in manufacturing processes.
Key components of modern manufacturing
The transition to Industry 4.0 isn’t a one-size-fits-all journey. Each manufacturer must evaluate its own needs and resources. Still, certain key components are essential for making this shift:
AI implementation
A significant portion of modern manufacturing facilities use AI to some extent. While some restrict its application to predictive maintenance that ensures uninterrupted production, others opt for full-scale AI optimization. This may involve:
- Enhancing production processes through data-driven decision-making.
- Identifying bottlenecks and optimizing workflows.
- Predictive maintenance, identifying potential equipment failures before they occur.
- Supply chain management, optimizing logistics, and reducing inefficiencies.
- Quality control, using machine vision to detect defects in real-time.
Successfully implemented, AI tackles issues most manufacturers struggle with, including:
- Excessive production: AI helps forecast demand more accurately, avoiding overproduction and reducing waste.
- High energy consumption: Rising energy costs and ESG reporting pressures compel manufacturers to optimize energy usage. AI identifies inefficiencies and suggests adjustments in real-time.
- Rising costs: AI optimizes raw material use and minimizes waste, contributing to overall cost savings.
Imagine an undetected defect in a conveyor motor powering a production line. If it malfunctions, a mid-sized cookie company could lose thousands of dollars in a single day due to halted production, missed orders, and labor costs. A shutdown costing $50,000 per day demonstrates how predictive AI maintenance pays for itself.
However, AI implementation comes with challenges, best tackled with professional data science development services. The AI-optimized smart factory requires:
- Data collection: Sensors, IoT devices, and reliable networks to capture production data.
- Data integration: Systems that unify disparate data streams for analysis.
- Qualified teams: Skilled workers trained in both AI technology and manufacturing processes.
Generative AI implementation
Generative AI differs from traditional AI in its ability to create new content and scenarios, making it valuable for specific manufacturing applications. Unlike traditional AI, which focuses on optimization and analysis, GenAI’s core strength lies in innovation.
While other sectors like e-commerce or banking absorbed GenAI quickly due to customer-facing applications, its manufacturing use cases are equally transformative:
- Automating design iterations and prototyping: For example, in the automotive industry, GenAI can simulate aerodynamics of car designs, reducing prototyping time.
- Enhancing supply chain planning and demand forecasting: By analyzing past trends and external variables, GenAI predicts supply chain disruptions and adjusts plans accordingly.
- Processing complex insights and decision-making: GenAI aids manufacturers in evaluating trade-offs between cost, time, and sustainability.
- Product discovery: For the pharmaceutical industry, GenAI identifies potential formulations for new drugs, expediting development.
Success metrics for GenAI implementation include reduced time-to-market, cost savings, and enhanced product innovation. If you are using generative AI services, they should be a foundation of your implementation.
Blockchain implementation
Although blockchain is rarely considered a core component of Industry 4.0, it plays a critical role in enhancing transparency and traceability—key elements of modern manufacturing.
How can blockchain support manufacturing?
- Supply chain transparency and provenance tracking: Blockchain securely records each step of the production process, ensuring authenticity and traceability.
- Smart contracts for automated vendor payments: Transactions are automated based on predefined conditions, reducing administrative overhead.
- Ensuring data integrity in quality assurance: Immutable records verify production compliance with stringent standards.
- Technology for reducing carbon footprint and environmental impact: Blockchain tracks carbon credits and ensures sustainable sourcing across the supply chain.
Why is the transition to Industry 4.0 inevitable?
Although the majority of manufacturers have yet to adopt the automated side of the force, this shift may soon become inevitable. The increasingly competitive market compels companies to innovate and automate according to Industry 4.0 principles, but there’s more to it than competition alone.
ESG goals
In Europe, Industry 4.0 represents a critical step towards ESG compliance. The reporting requirements introduced in 2024 demand advanced data collection across the entire supply chain, a task that is nearly impossible without leveraging AI. While these requirements currently apply to the largest players, they will expand to all sectors in the coming years. Enhanced traceability of raw materials and certain manufacturing processes ensures sustainable and compliant operations, driving adoption of state-of-the-art technologies like computer-aided manufacturing.
Labor shortages and skills gaps
In Q3 2024, U.S. manufacturing sector unit labor costs rose by 5.3%, following a 5.8% increase in Q2 2024. A shortage of skilled workers in both U.S. and European markets is pushing manufacturers to automate repetitive tasks and incorporate advanced technologies, including computer-aided design and edge computing, into their operations. Modern manufacturing workplaces are integrating these technologies to bridge the gap, as the industry struggles to fill well-paying positions like those in computer-integrated manufacturing.
Cost pressures and efficiency goals
A survey by BDO and Make UK revealed that 70% of UK manufacturers have faced cost increases of up to 20%, with 8% experiencing surges as high as 50%. Rising prices for raw materials, energy, and other inputs are driving manufacturers to adopt manufacturing strategies that focus on efficiency and waste reduction. Smart factories, enabled by state-of-the-art technologies, are reshaping assembly lines and repetitive manufacturing processes to achieve these goals.
Many market leaders understood the need of transitioning to Industry 4.0 early on. For instance, Bosch implemented IoT-enabled production lines and predictive maintenance based on a single cloud back in 2016. Unilever, on the other hand, leveraged AI and digital twins to optimize energy use in its factories, cutting CO2 emissions across manufacturing sites by 50%.
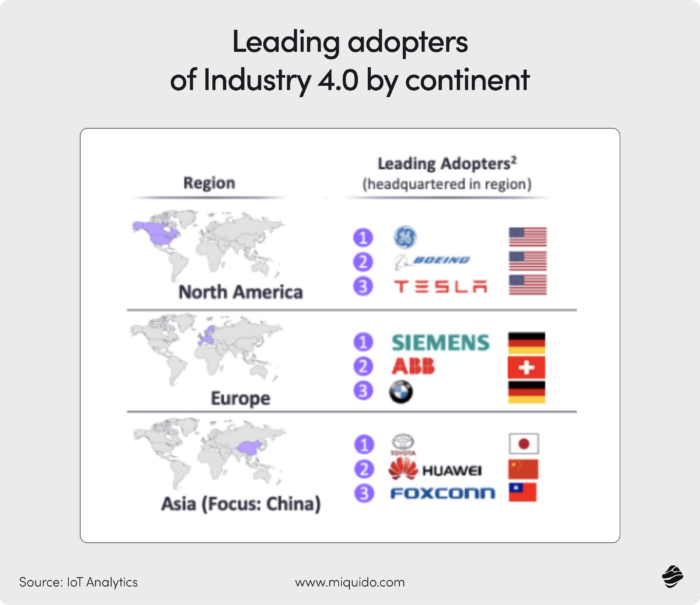
How lean management shaped modern manufacturing and industry 4.0
Lean management laid the foundation for modern manufacturing by emphasizing efficiency, waste reduction, and continuous improvement. Toyota’s adoption of lean practices spurred the development of automation, data-driven systems, and process standardization. These innovations not only enabled greater productivity but also paved the way for Industry 4.0.
Today, Industry 4.0 takes lean to the next level by integrating advanced technologies like IoT, AI, and robotics. These tools ensure that lean principles—such as waste reduction and flexibility—remain achievable in increasingly complex production environments. Companies embracing Industry 4.0 can maintain lean operations while scaling to meet global demands.
Lean management principles: A story of innovation
It all started in post-war Japan, when Toyota faced resource constraints and stiff competition. To survive, they developed lean management, focusing on eliminating waste (muda) and maximizing value. For instance, their Just-in-Time (JIT) system revolutionized inventory management by producing only what was needed, when it was needed.
The success of Toyota’s lean approach caught global attention. Companies in industries like aerospace and electronics adopted these principles, reaping benefits like reduced costs, faster delivery, and higher quality. Lean proved that continuous improvement could drive innovation across the manufacturing world.
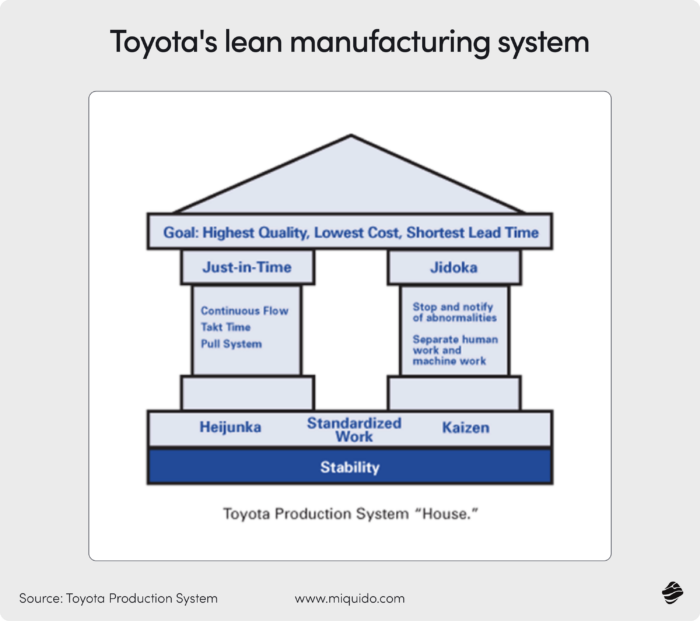
Lean’s impact on modern manufacturing
Lean principles directly influenced the advancements that define Industry 4.0 today:
- Automation and Robotics: Lean’s demand for efficiency inspired robotics and computer-aided manufacturing (CAM) to streamline repetitive tasks.
- Data-Driven Operations: Just-in-Time (JIT) fostered the development of IoT and sensors for real-time data tracking.
- Process Standardization: Lean’s focus on stability led to tools like Enterprise Resource Planning (ERP) systems.
- Collaborative Tools: Emphasis on teamwork encouraged technologies like cobots and communication platforms.
- Customer-Centric Solutions: Lean’s value-driven approach promoted innovations such as 3D printing and predictive logistics.
Good practices for modern manufacturing in 2025
Having all these aspects checked, you will bring your company one step closer to Industry 4.0. Our digital transformation services may help!
- Adopt lean principles with data-driven tools
- Use value stream mapping software to identify inefficiencies.
- Implement digital Kaizen boards to track continuous improvement initiatives.
- Standardize workflows using process automation platforms.
- Invest in IoT for predictive and real-time monitoring
- Deploy IoT sensors on machinery to monitor temperature, vibration, and usage.
- Use platforms to manage device data and enable real-time monitoring.
- Implement predictive maintenance algorithms to reduce downtime.
- Leverage AI and GenAI for smarter operations
- Use AI-powered scheduling tools to optimize production processes.
- Integrate generative AI for automating product design iterations.
- Train AI models to detect quality anomalies in real time.
- Implement blockchain for supply chain transparency
- Establish a secure record of supply chain transactions with blockchain systems.
- Enable smart contracts to automate supplier payments upon delivery verification.
- Track product origins and carbon emissions with blockchain-based solutions.
- Focus on sustainability with advanced metrics
- Install IoT-connected meters to monitor energy and water usage.
- Use carbon accounting software to measure and manage emissions.
- Replace traditional heating systems with waste heat recovery and integrate LED lighting to cut energy costs.
- Enhance employee training with AR and VR
- Use augmented reality headsets for immersive equipment training.
- Deploy virtual reality safety simulations to prepare employees for real-world scenarios.
- Offer upskilling courses focused on AI, IoT, and digital manufacturing.
- Integrate digital twins for process optimization
- Use digital twin platforms to model and simulate production environments.
- Monitor real-time performance through systems linked to digital twins.
- Simulate “what-if” scenarios to optimize layouts, materials, and logistics.
- Explore additive manufacturing to accelerate innovation
- Incorporate 3D printers for prototyping and small-scale production.
- Use software to optimize designs for additive manufacturing.
- Experiment with multi-material printing and recycled filaments to reduce waste and create eco-friendly products.