Over the past decades, the manufacturing industry has been a niche driving technological advancement. With globalization and increasing demand, automation has become a necessity.
Now, with the democratization of AI, the manufacturing industry is stepping into a new era. Industry 4.0 is not a new concept, but in 2025, it could take on a new dimension thanks to recent trends in manufacturing.
The guiding idea for 2025 in manufacturing?
In a nutshell: connecting the dots. The industrial metaverse integrates the potential of various technologies and maximizes the data available to manufacturing companies.
And beyond that? Efficiency and sustainability. Amid rising raw material and energy costs, companies are striving harder than ever to unlock savings and eliminate hidden expenses. Stricter regulations push them to closely monitor emissions throughout their supply chain and to embrace energy recovery practices.
Explore the strategies employed by manufacturing innovators to achieve these goals. Dive into the latest manufacturing innovations and technological trends in global supply chains that will shape 2025.
2025: The year of industrial metaverse
Real-time insights from interconnected systems are crucial in 2025, when every resource is precious and every downtime exposes companies to high costs.
Manufacturers employ various technologies but often lack a centralized system that enables optimization both locally and across global manufacturing sites.
Data integrity is another concern, creating vulnerabilities that hackers could exploit. Given that cyberattacks surged in 2024, there is no time to lose.
The answer? The industrial metaverse.
As a virtual environment, it integrates advanced technologies to enable seamless collaboration, optimization, and innovation in manufacturing.
Ideally, it integrates all these components:
- Data analysis: AI-powered tools transform raw data into actionable insights for better decision-making.
- Cloud computing: Centralized data storage and processing enable scalable operations and collaboration.
- IoT (Internet of Things): Real-time monitoring and communication between devices improve efficiency and accuracy.
- Digital twins: Virtual replicas of manufacturing systems simulate scenarios and predict outcomes.
- 5G: High-speed connectivity ensures low-latency communication and enhanced device interoperability.
- GenAI/AI: Automates design, improves predictive maintenance, and enhances workforce support.
- Edge computing: Processes data locally to minimize latency and ensure real-time system responses.
- Wearables: Augmented devices provide on-the-job assistance and real-time alerts to workers.
- Extended reality (XR): AR, VR, and MR enable immersive training, design collaboration, and maintenance.
- Blockchain: Ensures data security and trustworthiness, especially in supply chain tracking and transactions.
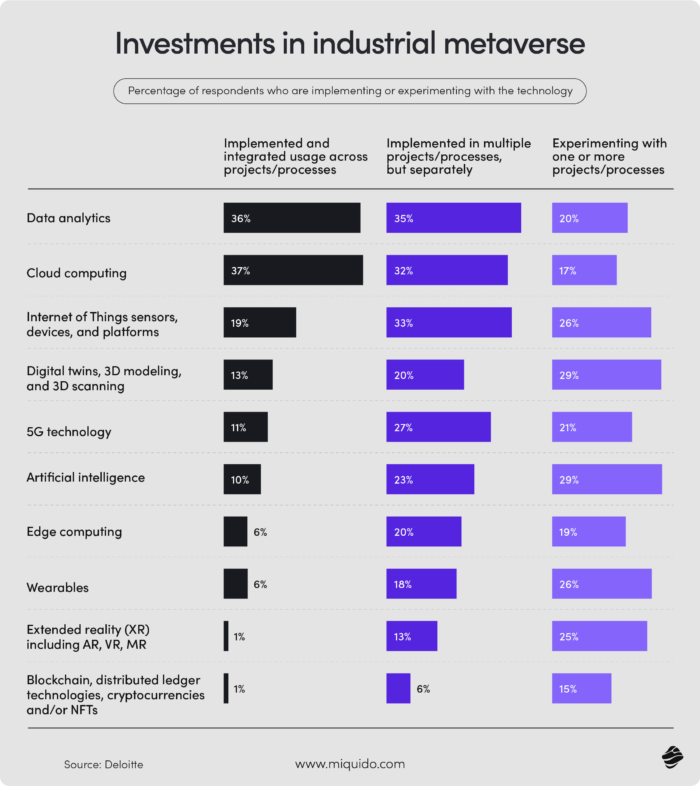
Recent trends in manufacturing to implement in 2025
Advanced additive manufacturing (3D printing)
Being subject to stringent regulations, 2025’s manufacturing industry must embrace a new norm: excessive material waste is no longer an option. This shift is driven not only by environmental awareness but also by cost considerations.
With every gram of CO2 emitted now monitored and reported in the EU, efficient material use has become essential. At the same time, growing demand for personalization and the fast pace of changing trends require highly flexible production methods.
The solution? 3D printing. Currently, it is primarily used in automotive and aerospace industries to produce lightweight, fuel-efficient components. However, it may soon become a universal solution for optimizing material use and reducing production costs.
The medical devices industry, where customization is a key requirement, has already embraced 3D printing extensively. This way, the prosthetics and other equipment leaving the manufacturing line can optimize the treatment to maximum.
Which sectors are next in line? There is immense potential in the construction industry, particularly for prefabricated components, as well as in consumer electronics.
GenAI-supported product design and development
2025 is the era of smarter, faster, and greener design in the manufacturing sector.
Manufacturing processes have long been burdened by slow design cycles and inefficient prototyping methods. Now, with industrial manufacturing trends demanding greater flexibility and sustainability, the need for innovation is critical.
GenAI offers a solution to these issues, transforming product design. It generates multiple design iterations within minutes, optimizing for materials, weight, and cost while incorporating advanced composites manufacturing innovation.
By prioritizing recyclable or minimal materials, GenAI aligns perfectly with the push for sustainable manufacturing processes.
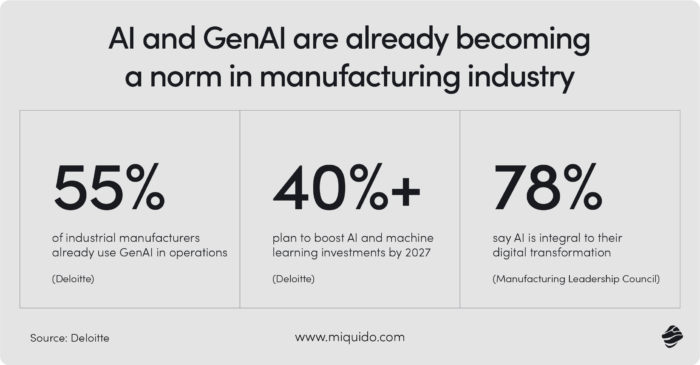
BMW is a standout example. Leveraging generative design tools like nTopology, the company developed lightweight components, including seat brackets, that are 50% lighter than traditional designs.
These innovations not only reduce material usage but also enhance supply chain resilience by cutting transportation costs.
Workforce augmentation with GenAI
The manufacturing sector is navigating unprecedented labor shortages.
By 2034, 1.9 million jobs could remain unfilled, according to the Manufacturing Institute and the National Association of Manufacturers. As experienced workers retire, manufacturers risk losing institutional knowledge vital for maintaining efficient operations and adopting smart manufacturing technologies.
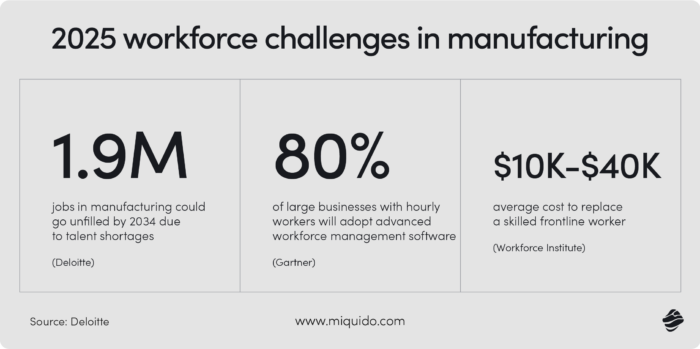
GenAI offers workforce development strategies that address these challenges. Immersive training simulations with custom GPT provide realistic environments for onboarding and upskilling manufacturing employees. On the shop floor, GenAI delivers predictive maintenance insights and real-time recommendations, helping operators make informed decisions quickly.
The benefits are clear: reduced errors, faster onboarding, and preserved knowledge for the next generation.
Digital twin integration for inventory
Visibility and adaptability are essential in supply chain management – especially now, that resources availability fluctuations and supply chain disruptions have intensified. Manufacturers face mounting pressure to optimize their supply chain resilience while embracing industrial internet capabilities.
Digital twins offer a powerful solution. These virtual replicas simulate inventory behavior, enabling predictive maintenance and optimized responses to demand changes.
Siemens exemplifies this approach. By integrating digital twins into its smart factories, the company minimizes delays caused by supply chain disruptions and improves overall inventory efficiency. This technology investment is revolutionizing inventory management across the manufacturing sector.
Drone and autonomous robot inventory audits
The era of manual inventory audits might be coming to an end.
Large-scale warehouses are grappling with labor shortages and the inefficiencies of traditional inventory counts. Time-consuming and error-prone, these methods are being replaced by advanced smart manufacturing technologies like autonomous drones and robots.
These systems perform real-time inventory monitoring, significantly improving accuracy while reducing labor costs. By integrating with the industrial internet and predictive maintenance tools, manufacturers can optimize inventory processes and prevent disruptions.
In the context of industrial manufacturing trends, drones and robots represent the future of inventory management, ensuring efficiency and accuracy at scale.
Life cycle analysis (LCA) software
Sustainability is now a non-negotiable priority for the manufacturing sector. ESG norms already cover the majority of EU manufacturers, and the other regions of the world may soon adopt similar unified regulations to fight climate crisis.
Assessing a product’s full environmental impact—across the supply chain and its lifecycle—is a challenge. With stricter regulations and growing consumer demand for eco-conscious products, manufacturers need effective solutions to meet these expectations.
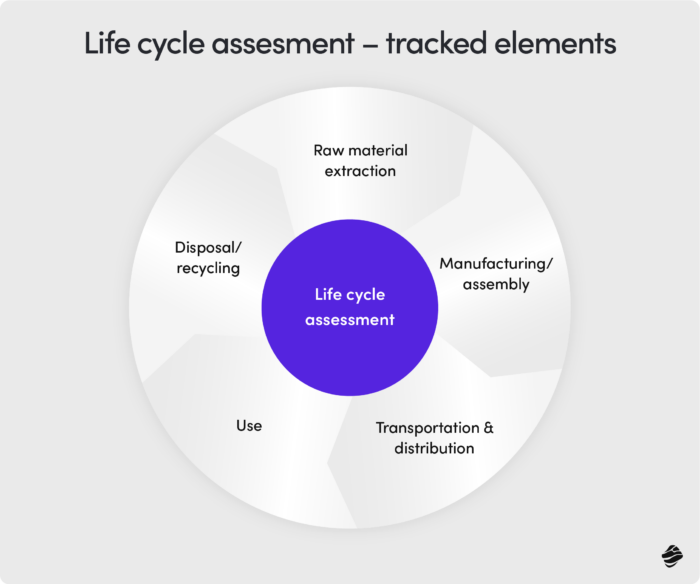
LCA software is a key enabler of this digital transformation, evaluating environmental impacts from raw material extraction to disposal. They empower manufacturers to identify opportunities for sustainability within their processes and align with advanced composites manufacturing innovation for greener solutions.
In a world where sustainability defines success, the adoption of LCA software underscores the manufacturing sector’s commitment to responsible innovation.
Smart lighting and climate control
Rising energy costs are a wake-up call for the manufacturing sector.
In 2024, energy prices surged by 16% in the EU and 9% in the US. For an average mid-sized manufacturing unit, annual energy consumption is approximately 1.2 million kWh.
This translates to an electricity bill of €288,000 in the EU (at an average of €0.24/kWh) or $144,000 in the US (at $0.12/kWh), highlighting the pressing need for energy efficiency.
Smart lighting and climate control systems provide a solution. IoT-controlled systems dynamically adjust LED lighting and HVAC (heating, ventilation, and air conditioning) based on occupancy and environmental factors. By implementing daylight harvesting systems, facilities can optimize natural light usage and minimize artificial lighting costs.
This shift isn’t just about cost-cutting—it’s a step toward sustainable manufacturing processes.
Energy harvesting systems
Every watt counts in 2025’s smart factories.
Wasted energy in industrial processes is a missed opportunity for efficiency. Energy harvesting systems capture residual energy—whether from heat, motion, or vibrations—and repurpose it effectively.
Energy management software takes this further by analyzing recovered energy and integrating insights into facility-wide operations. For example, recovered heat from industrial equipment can power other processes or be converted into electricity.
The result? Lower operational costs, reduced environmental impact, and a step toward supply chain resilience. These innovations reflect the manufacturing sector’s commitment to sustainability and smarter energy use, key pillars of digital transformation.
In 2025, energy harvesting systems will no longer be optional—they’ll be essential for maintaining competitive and efficient manufacturing facilities with net zero carbon emissions.
Supply chain tracking with blockchain
Blockchain is often associated with cryptocurrencies, but its true potential is gaining recognition in the manufacturing sector. Manufacturers and regulators are beginning to understand how this technology can transform supply chain management.
Blockchain functions as a decentralized ledger, where every transaction is a permanent, verifiable entry that cannot be altered. Imagine it as a shared diary that every participant can write in, but no one can erase or edit the past entries.
Through smart contracts—automated agreements coded into the blockchain—supplier verification and compliance tracking become seamless and secure.
Take a real-life example: a blockchain system ensures that every material used in a medical device has been sourced ethically and meets safety standards, without the need for expensive audits. This boosts trust among supply chain partners, reduces operational costs, and ensures compliance with stringent regulatory frameworks.
Autonomous logistics hubs with AI-driven orchestration
Modern supply chains face relentless pressure from shipping delays and labor shortages in transportation and warehousing. To address these challenges, AI-driven orchestration platforms are stepping in as game-changers.
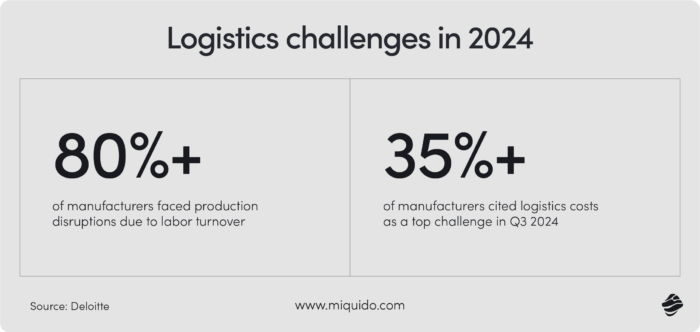
Picture a futuristic logistics hub powered by drones and autonomous vehicles. These machines handle last-mile delivery and streamline warehouse operations. Think of Amazon’s autonomous robot, Proteus. It works within warehouses to transport packages efficiently while interacting safely with human workers.
The results are remarkable: faster shipping times, significant labor efficiency, and reduced operational costs. These hubs are also scalable, meaning they can handle peak demands without requiring proportional increases in human labor. In an era where supply chain resilience is paramount, these innovations are no longer optional—they’re essential.
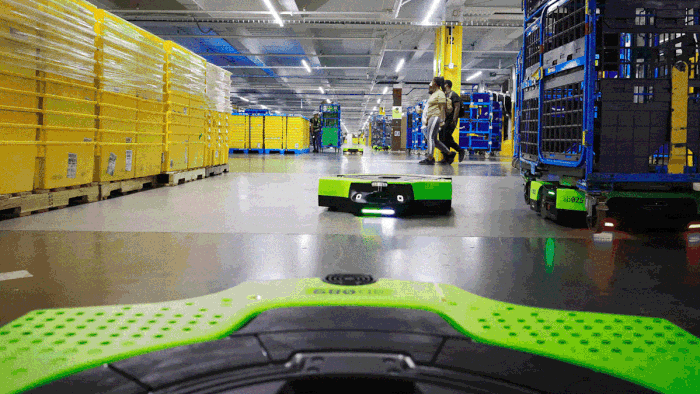
Recent trends in manufacturing – what will fuel innovation in 2025 and beyond?
As AI is increasingly regulated globally, advancements in legislation may define the pace of its innovation in manufacturing and beyond.
AI Act
The AI Act, which ensures transparency, safety, and ethics in AI systems, imposes additional requirements on AI implementers. In manufacturing, these apply to high-risk systems in automation, robotics, and supply chain management. Stricter data governance and risk assessment are required from such implementers. However, the majority of the AI innovations mentioned above do not fall into the high-risk category. This means that a slowdown in innovation due to the AI Act is unlikely.
Machine Directive updates
Machine Directive updates are another potential driver of change. They focus on aligning manufacturing equipment with modern safety and automation standards. IoT and AI for compliance can help meet these objectives, which could accelerate innovation adoption in the sector.
Carbon emissions regulations
Carbon border adjustment mechanisms could also speed up the adoption of sustainability software. Blockchain could facilitate maintaining transparency across the supply chain, and AI-supported systems could track and process emissions data, generating reports required by ESG regulations in the EU and recommending optimizations.
However, the main challenge remains the data. According to Deloitte’s report, issues with data quality, contextualization, and validation were identified as the primary obstacles to AI implementation by nearly 70% of surveyed manufacturing executives.
Manufacturing software tailor made for your needs
Industry 4.0 software development requires a blend of industry experience, technical skills and familiarity with recent trends in manufacturing. Let’s discuss how we can accommodate your needs and provide solutions that enhance productivity, cost-efficiency and safety.
Develop software that works like a well-oiled machine!