Let’s transport ourselves to an 80s factory floor. A manager hunches over a desk piled high with spreadsheets, schedules, and handwritten notes. Forecasting demand relies on historical sales figures, gut instincts, and a few lucky guesses. Adjusting production schedules is like solving a puzzle with missing pieces. Delays snowball, inventory piles up, and costs climb.
Fast forward a few decades, and the factory floor is a different world. AI oversees production planning, analyzing real-time inputs—demand trends, supply chain data, and equipment status. Forecasting is razor-sharp, driven by algorithms trained on oceans of data – no missed notes, no wasted materials. Orders shift instantly when a bottleneck arises, rerouting resources to prevent downtime.
Perfect image? If implemented well, AI planning can make the workflow in manufacturing companies as smooth as described above.
AI adoption in manufacturing has been intensifying in the recent years and will skyrocket in the next 10 years, as a statistics show. Just between 2024 and 2025, the AI market in manufacturing will almost double, if predictions prove right.
AI adoption for planning is one of the artificial intelligence innovations with the best investment to benefit ratio. All you need is quality data and its well-planned integration. Instead of time-consuming changes, you simply connect the dots and see your costs go down while delays disappear.
In this article, we break down AI for manufacturing planning and scheduling, understanding the mechanisms behind it and its main challenges.
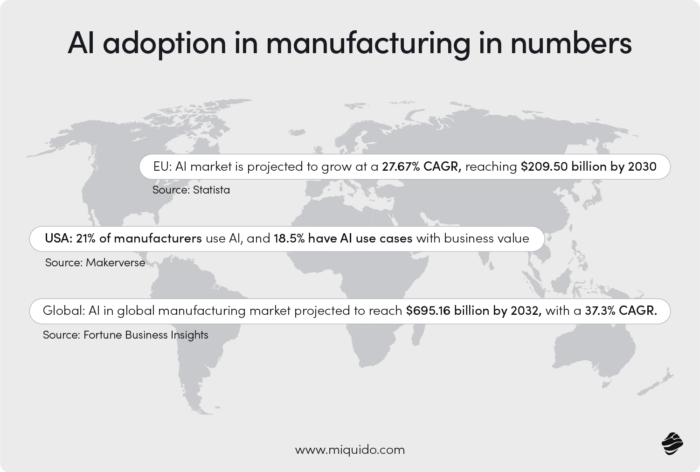
Combining algorithms for AI production planning
AI production planning software typically employs a combination of algorithms to address the multifaceted challenges of the production process. Each algorithm serves a specific purpose to optimize production costs and enhance production efficiency.
Neural networks, for instance, excel at handling nonlinear relationships and large datasets. Bayesian networks, on the other hand, effectively combine probabilities and causal relationships. Meanwhile, clustering algorithms are perfect for identifying hidden patterns in production or supply chain data.
That means, your software may rely on different models when analyzing complex factors influencing sales than when modeling supplier delays or segmenting production processes, and so on.
Whether you choose existing tools or bet on custom software development for better accuracy, you will probably rely on various AI algorithms.
Increasingly combined with natural language processing capacities, they can interpret data different formats, translating it to better insights.
AI applications in production planning
If searching for knowledge regarding production planning software, you are likely looking to optimize production schedules and avoid costs, waste, and timely downtimes. But good production scheduling software can do much more than that.
How can it support your overall production efficiency and fuel digital transformation?
Intelligent production scheduling techniques
A wave of last-minute order changes, equipment malfunctions, and fluctuating workforce availability – most middle-sized factories experience such difficulties every day. In such dynamic manufacturing environments, maintaining control over the production scheduling feels like an impossible task.
AI evaluates countless combinations faster than any human, ensuring that resources are allocated where they’re most effective. Machine performance, workforce shifts, order deadlines—based on all the production data, it generates schedules that adapt to constraints and prioritize efficiency.
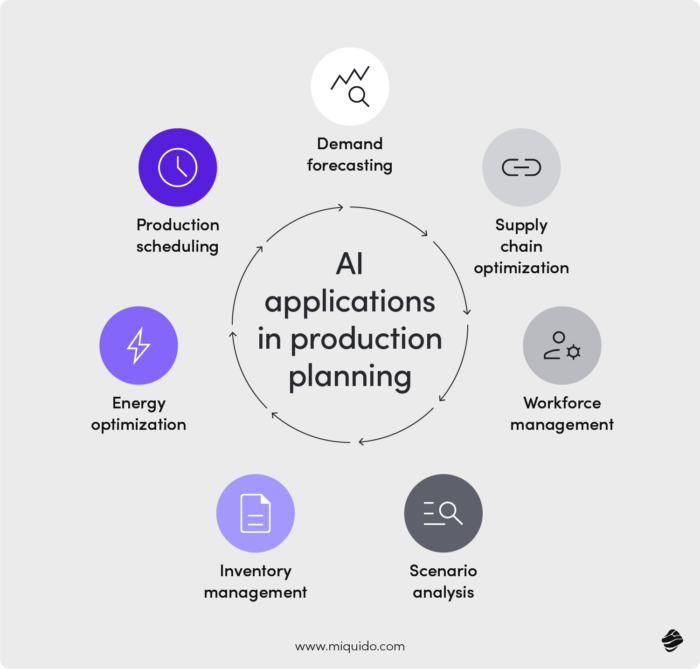
Real-time adjustments and flexibility
Think of this scenario: the workforce is prepped, and the assembly line is poised to start a new product launch. Suddenly, news arrives—a key supply chain route is blocked, and critical components won’t make it on time. Panic starts to set in as the entire manufacturing process is at risk of grinding to a halt.
AI and GenAI for production planning resolves such crises in the blink of an eye. It instantly assesses the impact of the delay, reroutes orders, identifies alternative suppliers, and recalibrates the production scheduling to keep operations moving forward.
Enhancing decision-making processes
Managing countless processes and working with multiple suppliers simultaneously makes it nearly impossible to see everything clearly. When it’s time to choose suppliers for a project that can’t afford any delays, plant managers often end up poring over spreadsheets, relying on gut feelings, and hoping for the best.
It doesn’t have to be this way if you have access to AI tools for production planning. By segmenting data, these systems identify patterns—such as which production lines handle specific product types most efficiently or which suppliers consistently cause supply chain disruptions. This enables managers to strengthen weak links, all while aligning with key production objectives.
The result? Decisions are informed, not improvised. Plant managers stop guessing and start executing with confidence, driven by actionable insights. They help the manufacturing industry optimize workflows, predict future demand, and maximize machine capacities.
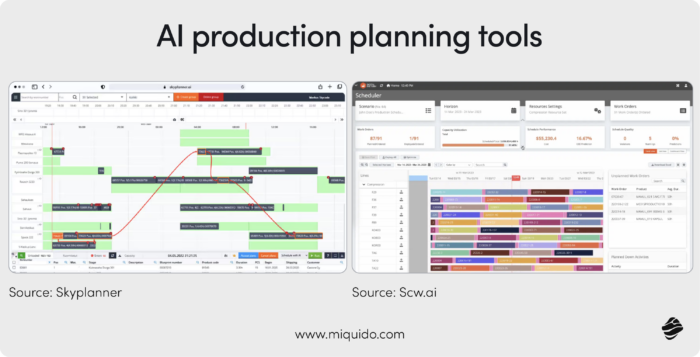
Benefits of AI in production planning
AI in production planning means working comfort, but the entire company benefits from it on many levels.
Think of all the variables a plant manager must consider when planning production. Many of these are entirely outside the company’s control and change dynamically—especially now, in an era of climate change and increasingly congested transport routes. Manual planning makes it impossible to respond to this dynamism. AI planning takes it head-on.
As a result, the productivity and efficiency of the production facility increase. There are no downtimes caused by a supplier failing to deliver a critical material on time. Even if unforeseen disruptions occur in the supply chain, AI immediately adjusts the schedule to the new reality. In such an optimized manufacturing unit, the problems of production surpluses and shortages are minimized.
Costs also decrease. The company does not unnecessarily reserve temporary workers and makes maximum use of available slots despite resource constraints. Resource utilization is optimized, which is particularly important for materials with limited shelf lives or specific storage requirements.
To-do list for AI production planning implementation
Implementing AI for production planning, you will have to face a series of challenges, as you would with any innovation. Your data has to be of good quality in order to provide you reliable insights. Many data sources from existing systems have to be well integrated. On top of that, your team needs training, because both too little and too much trust in AI can be a trap.
Instead of trying to avoid these challenges, just prepare yourself ahead of time. Forewarned is forearmed – our list will help you check all the boxes. Let it serve you as a roadmap, which, of course, has to be then adjusted to your specific challenges.
How to implement production planners successfully and prepare for operational constraints?
- Assess the quality and availability of:
- historical data (production, maintenance, inventory)
- real-time data (sensors, ERP systems).
- Map out integrations with existing systems:
- Enterprise resource planning (ERP), Manufacturing execution systems (MES), Supply chain management (SCM), Customer relationship management (CRM).
- IoT devices and middleware for machine data.
- Ensure sufficient computational resources:
- For large-scale operations: On-premise servers or cloud platforms (AWS, Azure, GCP).
- Connectivity: Stable network connections for real-time data.
- Train staff to interpret AI-generated insights.
- Adopt a phased approach:
- Pilot projects to test functionality.
- Gradual rollout to minimize disruption.
- Ensure data privacy and regulatory compliance.
- Implement robust security measures for sensitive production and employee data.
Data integration for AI production planning, step by step
There is no dynamic scheduling without successful data integration. The step-by-step guide below displays which systems and devices you should include and how to to that. When optimizing production plans with AI, you can treat this workflow as a framework.
Step 1: Collecting the data
Data collection is the foundation of AI-driven production planning. Machines send performance metrics through IoT sensors. ERP systems provide schedules, while supply chain platforms share inventory levels and delivery timelines. HR data adds information on employee shifts and skills.
Step 2: Integrating the data
Once collected, data from different sources must come together. This involves extracting raw data, cleaning and standardizing it, and storing it in a unified database. This step ensures seamless access to consistent information.
What could go wrong? Poorly standardized data might lead to mismatches or errors in processing. But with clear protocols and thorough quality checks, integration creates a solid foundation for AI models.
Step 3: Fusing the data
Data fusion merges disparate datasets into one coherent model. Real-time machine updates combine with historical schedules to highlight delays. Employee availability adjusts resource allocation dynamically. This step links the dots across operations.
What to pay attention to? Misaligned data sources may result in gaps or redundancies. However, it’s all a matter of well-designed pipelines.
Step 4: Feature engineering
Now it’s time to transform data into meaningful inputs for AI models. For example, machine downtime rates, material lead times, or employee productivity indices are computed. These features allow AI to understand the nuances of the production process.
Step 5: Model training
Prepared datasets are fed into AI models to uncover patterns and optimize processes. A reinforcement learning model might adjust schedules for efficiency, while another predicts machine failures.
Step 6: Insights generation
AI turns processed data into actionable insights. Prediction models forecast delays or resource shortages, while optimization models suggest adjustments to schedules, inventories, or machine usage. Dashboards display these insights in real time..
Step 7: Feedback loop
The final step ensures continuous improvement. Production outcomes and user feedback are fed back into the system. This updates the AI models, refining their predictions and keeping them aligned with evolving conditions.
AI for planning and scheduling – success stories
Well-implemented AI-powered scheduling can give a company a significant boost. Here are two success stories that prove this approach pays off.
BMW
At BMW, AI scheduling is part of the broader BMW iFactory strategy. As part of this initiative, the company created digital twins of their factories, enabling virtual planning and real-time collaboration across locations.
This ensures maximum efficiency in AI production planning. All system and sensor data remain internal. Through visualization in digital twins, plant managers gain a better understanding of what’s happening both locally and globally.
Result? Reduced planning time, optimized investments, stable product launches, and efficient processes.
Lenovo
At Lenovo, implementing AI for production planning delivered measurable and impressive results. The company developed an in-house AI-powered Advanced Production Scheduling (APS) system to optimize its supply chain.
This implementation led to a 24% increase in production line capacity, a 19% rise in production volumes, and a 3.5-fold improvement in on-time deliveries.
Benefit from AI for production planning
What’s the takeaway? While there are exceptions, in most cases, custom software development delivers more substantial benefits. Developing a production scheduling solution from scratch allows companies to account for variables specific to their operations, such as raw material constraints or industry-specific regulations.
Need support with manufacturing software development or data integration? Let’s discuss your needs and find the best solution for you. Whether you need a new system or legacy app modernisation, we can help!